ZCMC ACTIVITY
ZCMC CJSC operates the Kajaran deposit as an open pit mine, with significant proven and probable reserves and produces 22 million tonnes of ore per year.
EXPLORATION
GEOLOGICAL SETTING OF KAJARAN DEPOSIT
The industrial material of the deposit is located on the eastern side of the north-west oriented (320-340ᴼ) Tashtun fault, which dips at approximately 45 degrees to the east-north-east.
MINING
Mining activities are carried out in accordance with modern industry standards
Currently the extraction works in the open pit are carried out in the horizontal range of 1890-2130 m.
Drilling and blasting techniques are used for the extraction of ore and waste in the mine, after which the ore is transported to the primary crusher either via in-pit ore pass and rail haulage or directly by trucks.
Waste is transported to the waste storage facility by trucks.
Copper content
in mined ore
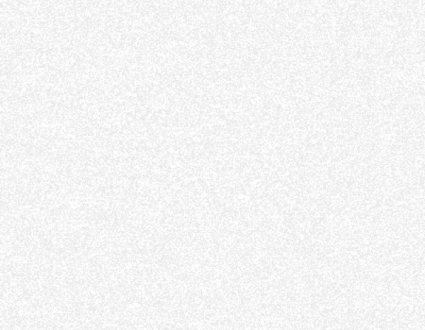
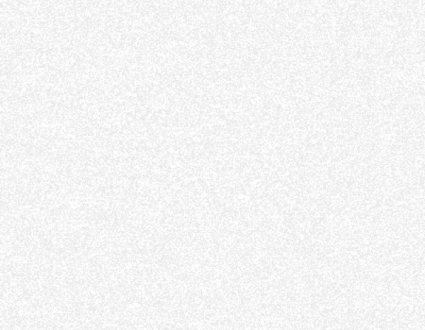
Molybdenum content
in mined ore
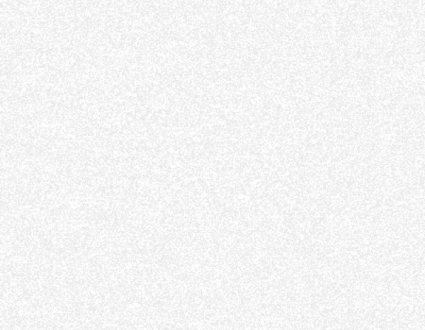
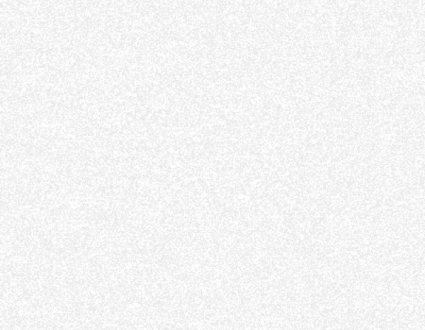
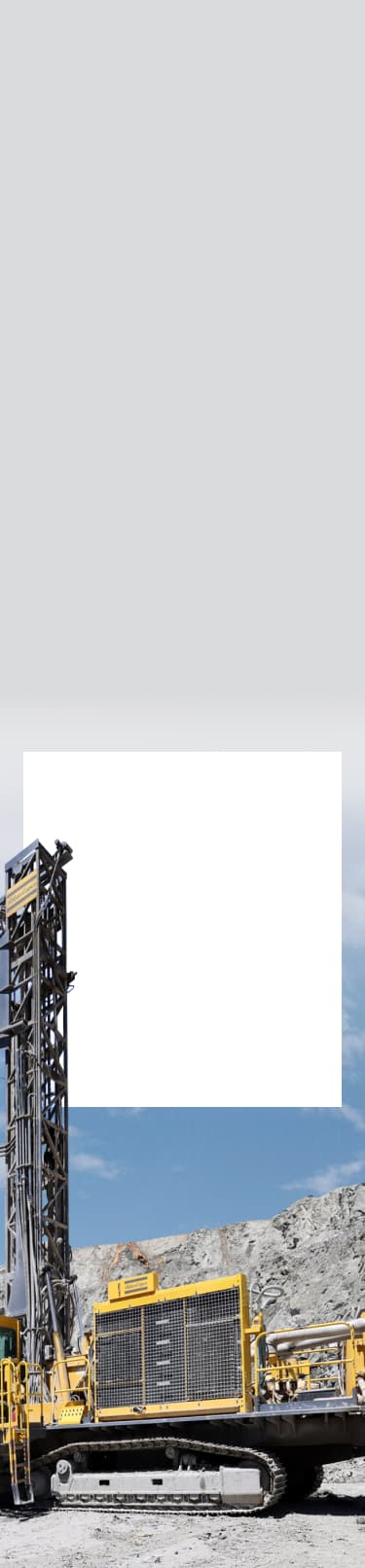
Advantages
Our Advantages
Allows for high quality production and expansion
High professional knowledge of employees
High professional knowledge of employees
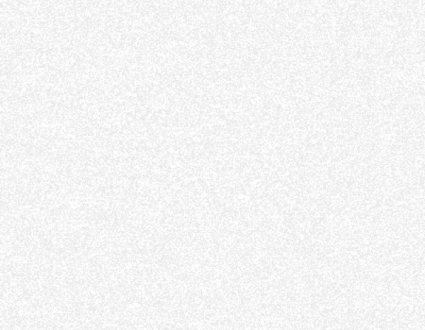
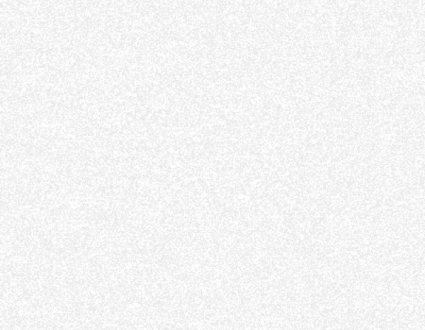
Long-standing traditions of the mining region
Long-standing traditions of the mining region
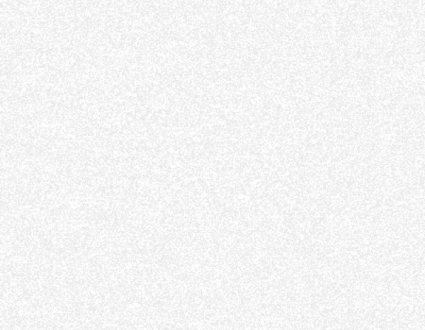
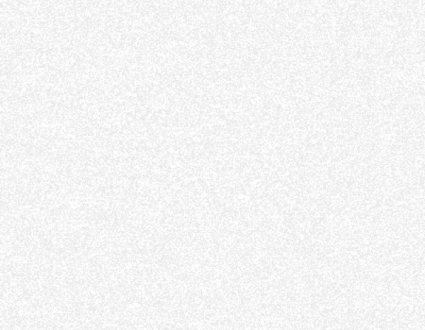
Competent management
Competent management
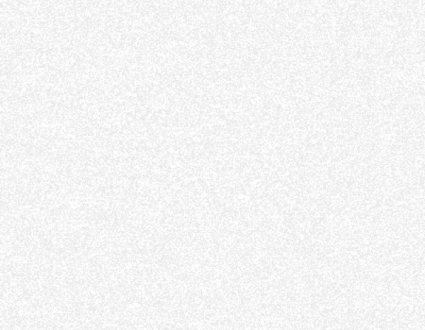
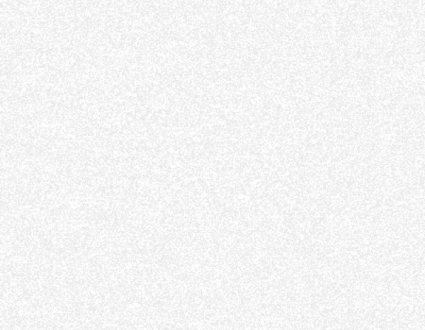
Solid corporate culture
Solid corporate culture
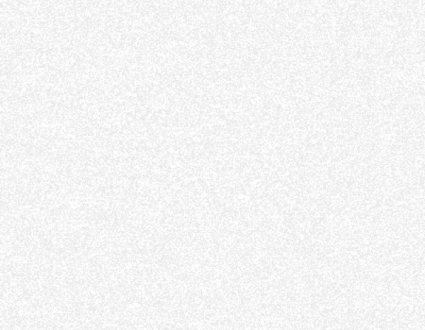
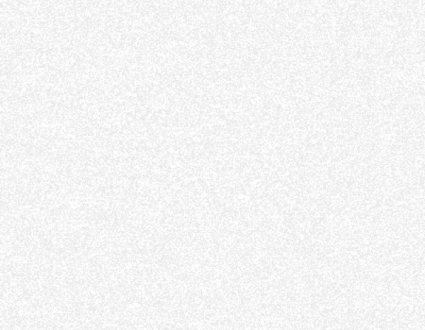
PROCESSING
We produce molybdenum and copper concentrates
Crushing
From the open pit, ore lumps, up to 1200 mm, are delivered to the primary crushing plant. Running through three-stage crushing – large, medium and small – the ore is reduced to 18-22 mm; thereafter it is ground in mills and processed. Part of it, after the first crushing stage, in maximum size of 300 mm, is conveyed to the semi autogenous grinding mill.
Grinding
Semi autogenous grinding unit is the most important component of the preparation for enrichment. The gigantic mills of this unit have been manufactured in the USA, hence these mills are often referred to as “Americans” at the ZCMC; their performance exceeds similar mills ever operated elsewhere at the ZCMC.
Enrichment
At the enrichment plant, crushed ore is processed by traditional methods flotation. Flotation sequentially includes collective flotation of copper and molybdenum, and selective flotation where molybdenum minerals are separated from collective concentrate. Copper and molybdenum concentrates are thickened and filtered at separate plants.
Quality Control
Quality control is carried out by the Quality Control Department, in chemical and metallurgical laboratories, which are furnished with modern equipment.
Tailings Management
The mining and processing of ore also includes safe transportation of beneficiation residues (tailings) and their storage at the Artsvanik tailings storage facility, located approximately 27 km from the enrichment plant in a straight line.
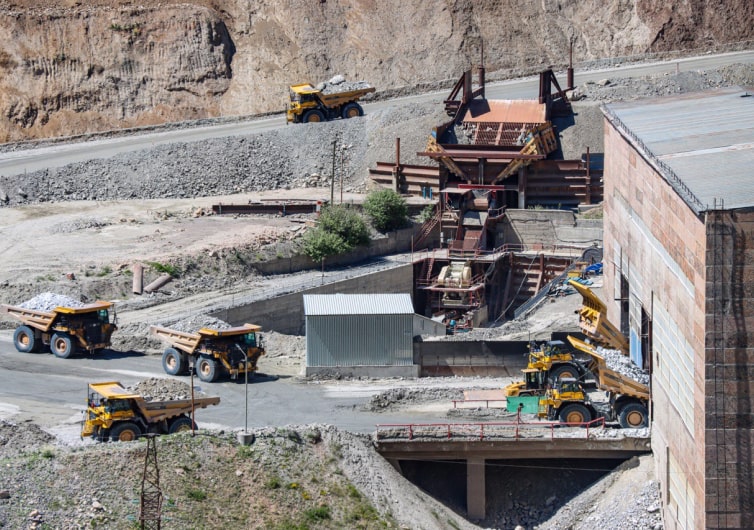
Crushing
From the open pit, ore lumps, up to 1200 mm, are delivered to the primary crushing plant. Running through three-stage crushing – large, medium and small – the ore is reduced to 18-22 mm; thereafter it is ground in mills and processed. Part of it, after the first crushing stage, in maximum size of 300 mm, is conveyed to the semi autogenous grinding mill.
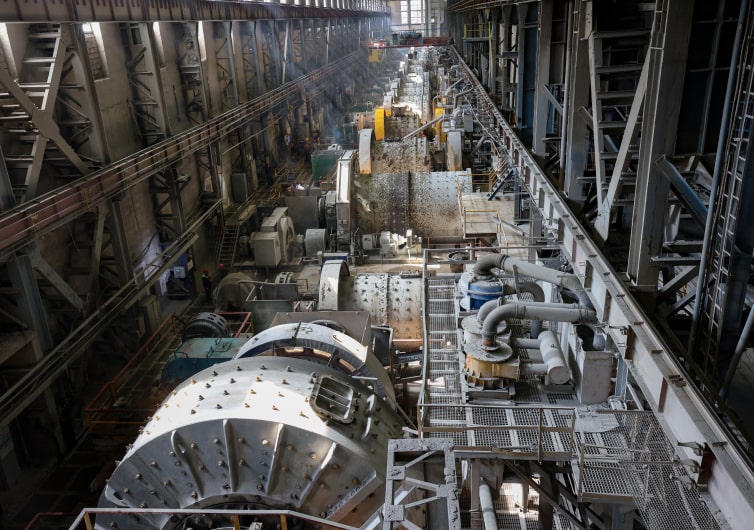
Grinding
Semi autogenous grinding unit is the most important component of the preparation for enrichment. The gigantic mills of this unit have been manufactured in the USA, hence these mills are often referred to as “Americans” at the ZCMC; their performance exceeds similar mills ever operated elsewhere at the ZCMC.
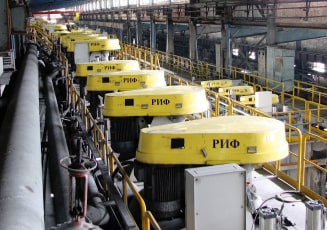
Enrichment
At the enrichment plant, crushed ore is processed by traditional methods flotation. Flotation sequentially includes collective flotation of copper and molybdenum, and selective flotation where molybdenum minerals are separated from collective concentrate. Copper and molybdenum concentrates are thickened and filtered at separate plants.
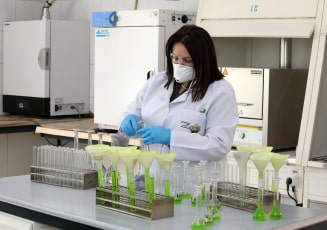
Quality Control
Quality control is carried out by the Quality Control Department, in chemical and metallurgical laboratories, which are furnished with modern equipment.
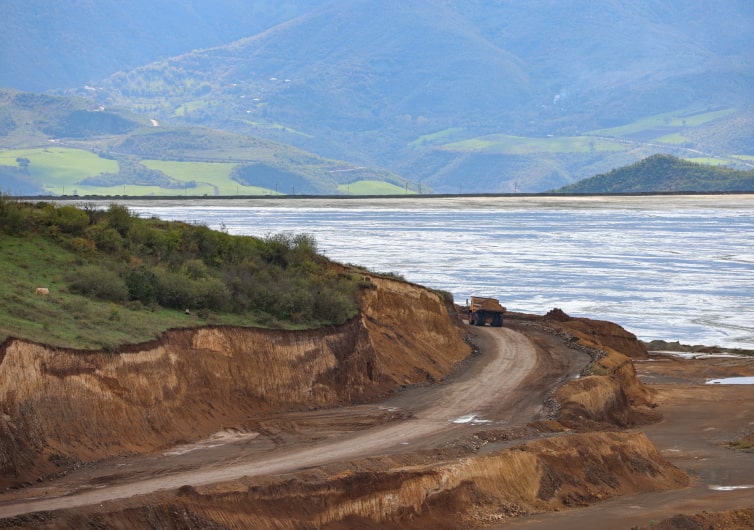
Tailings Management
The mining and processing of ore also includes safe transportation of beneficiation residues (tailings) and their storage at the Artsvanik tailings storage facility, located approximately 27 km from the enrichment plant in a straight line.